In today's fast-paced industrial landscape, precision custom components have become indispensable for businesses seeking to enhance efficiency, reduce costs, and improve product quality. These specialized parts, designed and manufactured to meet exact specifications, play a critical role in various industries, from automotive to aerospace and medical devices. As technology continues to evolve, the demand for high-precision components tailored to specific needs is growing exponentially.
The ability to create custom components with exact dimensions and tolerances is transforming how companies operate. By investing in precision manufacturing, businesses can achieve better performance, reliability, and longevity in their products. This article delves into the world of precision custom components, exploring their significance, applications, and the technologies driving this industry forward.
Whether you're an engineer, manufacturer, or business owner, understanding the nuances of precision custom components can provide a competitive edge. In this comprehensive guide, we'll cover everything you need to know about this critical aspect of modern manufacturing, including the latest trends, best practices, and industry insights.
Read also:Idea Ingram Hills A Comprehensive Guide To Discovering Hidden Gems
Table of Contents
- What Are Precision Custom Components?
- The Importance of Precision in Manufacturing
- Industries Utilizing Precision Custom Components
- Technologies Driving Precision Manufacturing
- The Design Process for Precision Components
- Materials Used in Precision Manufacturing
- Quality Control in Precision Custom Components
- Cost Considerations in Precision Manufacturing
- Future Trends in Precision Custom Components
- Choosing the Right Partner for Precision Manufacturing
What Are Precision Custom Components?
Precision custom components refer to parts and assemblies manufactured to exact specifications, tailored to meet the unique requirements of a particular application or industry. Unlike standard, off-the-shelf components, these parts are designed and produced using advanced technologies and processes to ensure unparalleled accuracy and reliability.
These components are essential in industries where failure is not an option, such as aerospace, medical devices, and automotive manufacturing. Precision custom components are often used in critical applications where even the slightest deviation from specifications can lead to catastrophic consequences.
Key Characteristics of Precision Custom Components
Precision components are distinguished by several key characteristics:
- High Accuracy: Tolerances as low as a few micrometers ensure perfect fit and function.
- Material Integrity: Components are made from materials chosen for their specific properties, such as strength, durability, or resistance to extreme conditions.
- Complex Geometries: Advanced manufacturing techniques enable the creation of intricate shapes and designs that would be impossible with traditional methods.
- Consistency: Every component produced meets the same exacting standards, ensuring uniformity across batches.
The Importance of Precision in Manufacturing
Precision is crucial in modern manufacturing, especially when dealing with custom components. The ability to produce parts with exact dimensions and tolerances directly impacts the performance, reliability, and lifespan of the final product. In industries like aerospace and medical devices, precision is not just a preference—it's a necessity.
For example, in the aerospace industry, precision custom components are used in jet engines, landing gear, and control systems. Even the smallest deviation from specifications can compromise the safety and efficiency of an aircraft. Similarly, in the medical field, precision components are used in life-saving devices such as pacemakers, surgical instruments, and diagnostic equipment.
Benefits of Precision Manufacturing
- Improved Performance: Components that fit perfectly enhance the overall performance of the final product.
- Enhanced Reliability: Precision ensures that components function consistently over time, reducing the risk of failure.
- Increased Efficiency: Accurate components reduce waste and improve production processes.
- Cost Savings: While precision manufacturing may involve higher upfront costs, the long-term savings from reduced downtime and improved product quality often outweigh the initial investment.
Industries Utilizing Precision Custom Components
Precision custom components are used across a wide range of industries, each with its own specific requirements and applications. Below are some of the key industries that rely heavily on precision manufacturing:
Read also:Itsnatdog Onlyfans Leaked The Controversy And Facts You Need To Know
Automotive Industry
The automotive industry uses precision components in engines, transmissions, braking systems, and suspension systems. As vehicles become more advanced, the demand for high-precision parts continues to grow. Electric vehicles (EVs), in particular, require components with exacting tolerances to ensure optimal performance and energy efficiency.
Aerospace Industry
In aerospace, precision custom components are used in everything from aircraft engines to avionics systems. The ability to produce parts with exact dimensions and tolerances is critical for ensuring the safety and reliability of aircraft.
Medical Devices
The medical device industry relies on precision components for everything from surgical instruments to implantable devices. These components must meet strict regulatory standards and be produced with the highest level of accuracy to ensure patient safety.
Technologies Driving Precision Manufacturing
Advances in technology have revolutionized the field of precision manufacturing, enabling the production of components with unprecedented accuracy and complexity. Below are some of the key technologies driving this industry forward:
CNC Machining
Computer Numerical Control (CNC) machining is one of the most widely used technologies in precision manufacturing. CNC machines use computer-controlled tools to cut, shape, and finish materials with exact precision. This technology allows for the production of complex geometries and intricate designs that would be impossible to achieve with manual methods.
3D Printing
Also known as additive manufacturing, 3D printing has emerged as a game-changer in the production of precision custom components. This technology enables the creation of complex parts layer by layer, offering unparalleled design flexibility and reducing material waste.
Robotics
Robotics is increasingly being used in precision manufacturing to automate repetitive tasks and improve accuracy. Robots can perform tasks with consistent precision, reducing the risk of human error and improving production efficiency.
The Design Process for Precision Components
The design process for precision custom components involves several critical steps, each requiring careful attention to detail. Below is an overview of the typical design process:
Step 1: Requirements Analysis
The first step in the design process is to analyze the requirements of the application. This involves understanding the specific needs of the customer, including the desired functionality, performance, and environmental conditions the component will be subjected to.
Step 2: Material Selection
Choosing the right material is critical for ensuring the component meets the required specifications. Factors such as strength, durability, corrosion resistance, and thermal properties must be considered when selecting materials.
Step 3: Prototyping
Once the design is finalized, a prototype is created to test the component's performance and identify any potential issues. Prototyping allows for early detection of design flaws and ensures that the final product meets all requirements.
Materials Used in Precision Manufacturing
Precision custom components are made from a wide range of materials, each chosen for its specific properties. Below are some of the most commonly used materials in precision manufacturing:
Metals
Metals such as steel, aluminum, titanium, and stainless steel are widely used in precision manufacturing due to their strength, durability, and resistance to extreme conditions.
Plastics
Plastics are increasingly being used in precision components, particularly in applications where weight reduction is a priority. Advanced polymers and composites offer excellent mechanical properties and can be tailored to meet specific requirements.
Ceramics
Ceramics are used in applications requiring high temperature resistance, wear resistance, and electrical insulation. These materials are ideal for components used in harsh environments.
Quality Control in Precision Custom Components
Quality control is essential in precision manufacturing to ensure that every component meets the required specifications. Below are some of the key quality control measures used in this industry:
Inspection Techniques
Advanced inspection techniques such as coordinate measuring machines (CMMs) and optical inspection systems are used to verify the accuracy of components. These tools can detect even the smallest deviations from specifications, ensuring that every part meets the required standards.
Statistical Process Control
Statistical process control (SPC) is used to monitor and control the manufacturing process, ensuring consistency and reducing variability. By analyzing data from the production line, manufacturers can identify and address potential issues before they impact product quality.
Cost Considerations in Precision Manufacturing
While precision custom components offer numerous benefits, they can also come with higher costs compared to standard components. Below are some of the key cost considerations in precision manufacturing:
Material Costs
The cost of materials can vary significantly depending on the type of material used and its availability. High-performance materials such as titanium and advanced polymers can be more expensive than standard materials.
Tooling Costs
Tooling costs can be significant, particularly for complex components requiring specialized tools and fixtures. However, these costs can often be offset by the improved efficiency and reduced waste achieved through precision manufacturing.
Future Trends in Precision Custom Components
The future of precision manufacturing looks promising, with several emerging trends set to shape the industry:
Industry 4.0
The integration of digital technologies, such as the Internet of Things (IoT) and artificial intelligence (AI), is transforming the manufacturing landscape. Smart factories equipped with connected machines and systems enable real-time monitoring and optimization of production processes.
Sustainability
Sustainability is becoming an increasingly important consideration in manufacturing. Companies are exploring ways to reduce waste, improve energy efficiency, and use environmentally friendly materials in the production of precision components.
Choosing the Right Partner for Precision Manufacturing
Selecting the right partner for precision manufacturing is critical for ensuring the success of your project. Below are some factors to consider when choosing a manufacturing partner:
Experience and Expertise
Look for a partner with extensive experience in precision manufacturing and a proven track record of delivering high-quality components. Their expertise can help ensure that your project is completed on time and within budget.
Technological Capabilities
Ensure that the partner has access to the latest technologies and equipment necessary for producing precision custom components. This includes CNC machines, 3D printers, and advanced inspection tools.
Conclusion
Precision custom components are a vital part of modern manufacturing, enabling businesses to create products with unparalleled accuracy and reliability. By understanding the importance of precision, the technologies driving this industry, and the key considerations in choosing a manufacturing partner, companies can harness the full potential of precision manufacturing.
We invite you to share your thoughts and experiences with precision custom components in the comments section below. Additionally, feel free to explore our other articles for more insights into the world of manufacturing and technology. Thank you for reading, and we look forward to hearing from you!
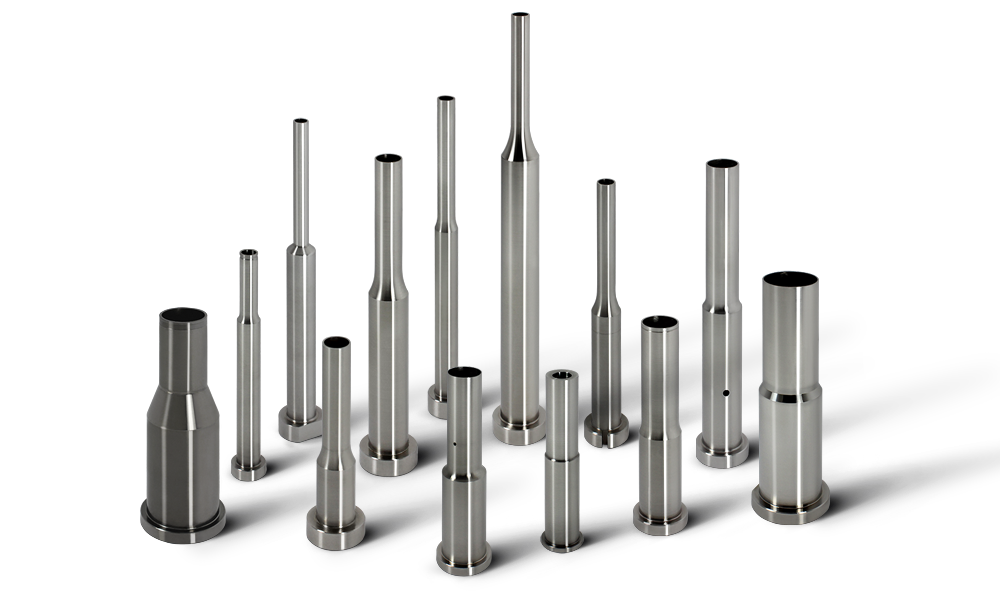